Enhance Equipment
Reliability with
Predictive Maintenance
Our Predictive Maintenance solutions
utilize IoT sensors
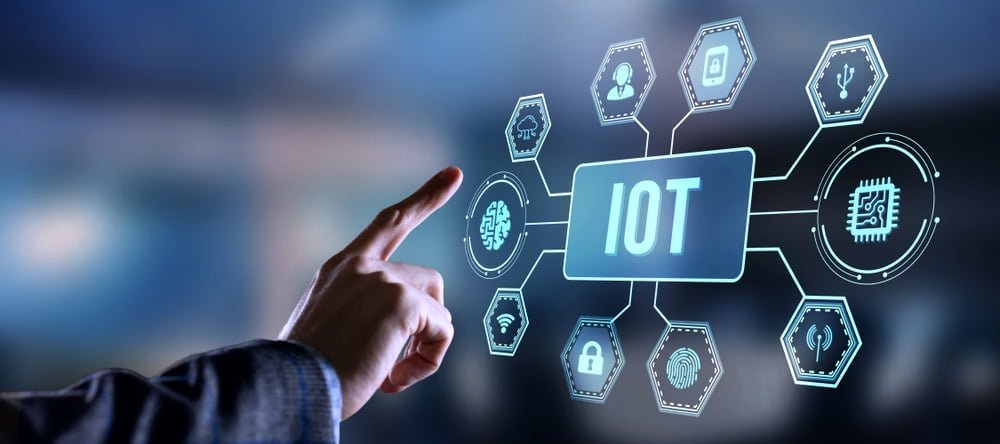
Overview
Unplanned equipment failures can lead to costly downtime and disruptions. Our Predictive Maintenance solutions utilize IoT sensors, machine learning, and predictive analytics to identify potential issues before they occur. By implementing predictive maintenance strategies, businesses can reduce maintenance costs, maximize equipment uptime, and extend the lifespan of critical assets.
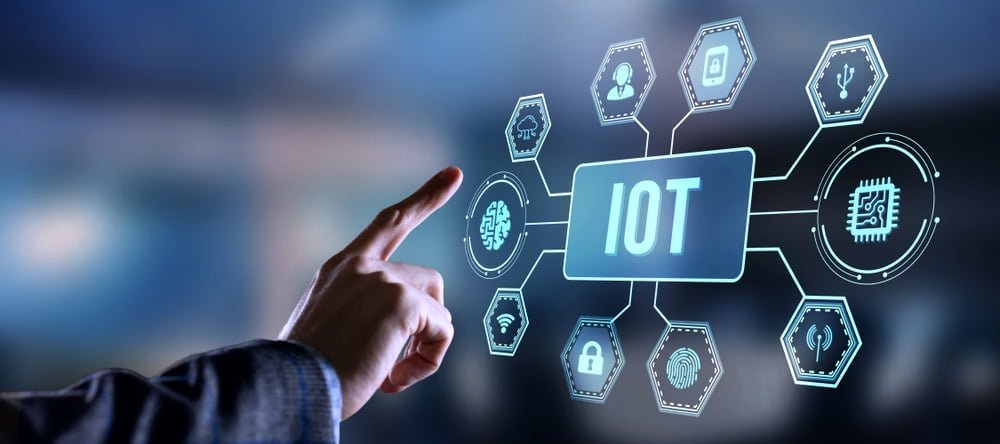
IoT Sensor Integration
Our Predictive Maintenance solutions leverage IoT sensors to collect real-time data on equipment performance, operating conditions, and environmental factors. By integrating these sensors into your machinery, you can monitor key parameters and gather valuable insights for predictive maintenance.
Machine Learning Algorithms
Using advanced machine learning algorithms, our solutions analyze historical data and identify patterns or anomalies that indicate potential equipment failures. By training the models with relevant data, the system becomes more accurate in predicting maintenance needs and identifying early warning signs.
Condition Monitoring
With predictive maintenance, you can continuously monitor the condition of your equipment in real-time. IoT sensors track various parameters such as temperature, vibration, pressure, and lubrication levels, providing insights into the health and performance of critical assets.
Anomaly Detection
By comparing real-time data with baseline patterns, our predictive maintenance solutions can identify deviations or abnormalities that may signify impending equipment failures. This enables proactive maintenance actions to be taken before major breakdowns occur.
Maintenance Planning and Scheduling
Predictive maintenance helps optimize maintenance planning and scheduling. By predicting the remaining useful life of equipment and estimating maintenance requirements, you can plan maintenance activities more effectively, reduce downtime, and minimize disruption to operations.
Cost Reduction
By adopting predictive maintenance strategies, businesses can significantly reduce maintenance costs. By focusing on proactive maintenance and addressing issues in their early stages, you can avoid costly emergency repairs, optimize spare parts inventory, and maximize the lifespan of critical assets.
Improved Equipment Uptime
Predictive maintenance minimizes unplanned downtime by detecting and addressing potential issues before they lead to equipment failures. This ensures that your machinery operates at optimal levels, enhancing overall productivity and reducing production losses.
Data-Driven Insights
Predictive maintenance solutions generate valuable data-driven insights that can be used for continuous improvement. By analyzing the data collected from IoT sensors and maintenance records, you can identify trends, optimize maintenance strategies, and make informed decisions to enhance equipment reliability.
Remote Monitoring and Alerts
With predictive maintenance, you can remotely monitor equipment health and receive real-time alerts when anomalies or potential failures are detected. This enables timely intervention, regardless of the geographical location of your assets, and minimizes the need for on-site inspections.
Asset Performance Optimization
By proactively addressing maintenance needs and optimizing equipment performance, predictive maintenance contributes to overall asset performance optimization. It helps extend the lifespan of critical assets, improve reliability, and achieve higher operational efficiency.
What Our Customers Say
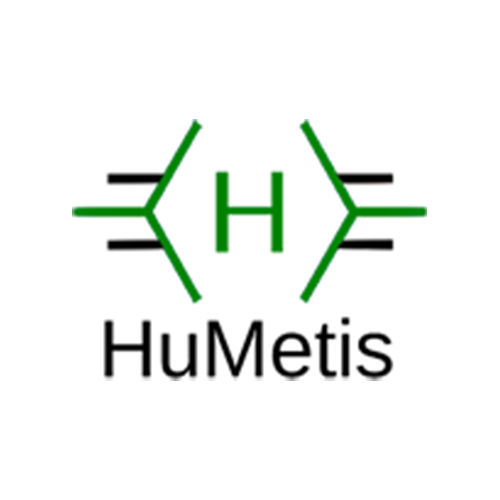
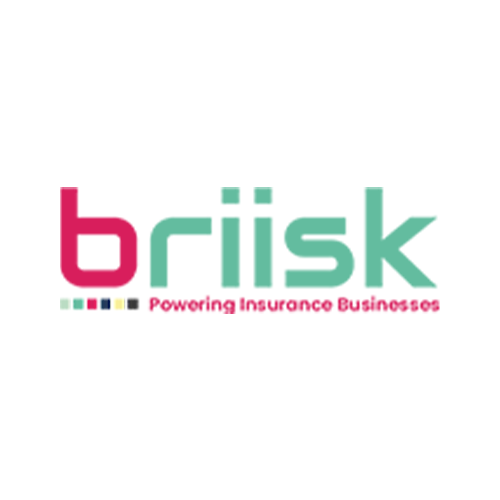
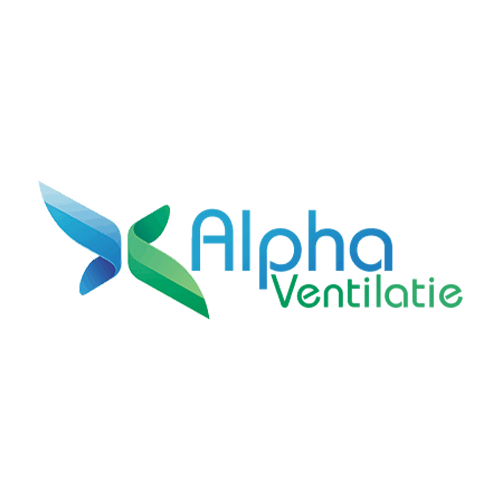
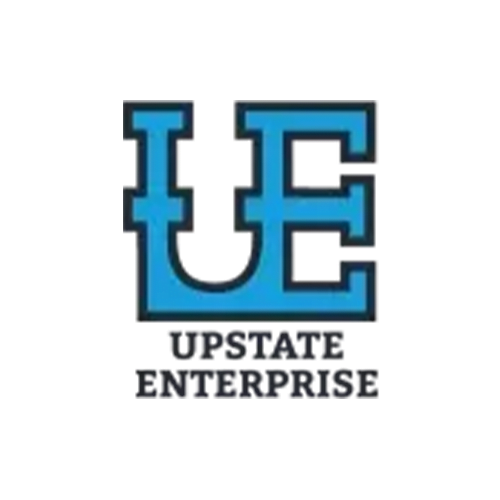
