Introduction
In recent years, drones or unmanned aerial vehicles (UAVs) have seen rapid adoption across various industries for inspection and surveillance purposes. Equipped with cameras and sensors, drones can capture images and videos from unique aerial perspectives that are difficult or dangerous for human inspectors to access. This has opened up new possibilities for automating visual inspection tasks like infrastructure monitoring, precision agriculture analysis, and mapping services.
One particularly promising application of drone technology is integrating computer vision techniques to enable autonomous inspections. By leveraging AI and deep learning algorithms, drones can automatically detect defects, damages, anomalies, etc. without needing a human reviewer to constantly monitor the video feed. This provides huge time and cost savings compared to traditional manual inspection processes. In this post, we will go through a step-by-step guide on developing a DIY drone system for computer vision-based infrastructure inspections.
AI and Computer Vision Algorithms
A key enabling technology for autonomous drone inspections is artificial intelligence and deep learning for robust computer vision capabilities. The software models powering the defect detection, classification and predictive analytics need to be highly accurate and reliable before large-scale deployment.
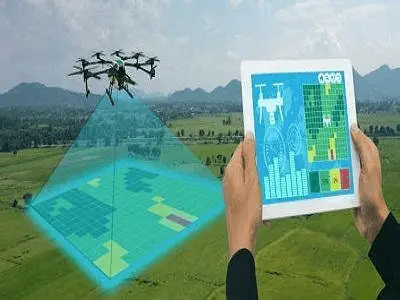
Convolutional Neural Networks
Powerful convolutional neural networks (CNN) are widely used for image classification and object detection tasks in the field of computer vision. CNN algorithms contain multiple layers to extract high-dimensional features from images to identify complex patterns automatically. These networks need to be trained on thousands of sample images of infrastructure assets like bridges, wind turbines, solar farms, etc. The training images need to have labeled examples of defects like cracks, corrosion, missing bolts, pest damages, and other anomalies for the CNN to learn from.
Data augmentation and libraries
Data augmentation techniques, such as crops, flips, and rotations, help to virtually increase the size of training datasets. Open source libraries such as OpenCV make it easier to create data loaders, pre-processing pipelines, and neural network architectures without requiring extensive coding. Modern object detectors, such as YOLOv8, can identify hundreds of defect types from high-resolution drone footage in real time. The trained models perform inference at breakneck speed on embedded hardware such as Nvidia Jetson boards.
Enhanced Defect Detection
By combining infrared, and thermal sensors alongside RGB cameras, drones can provide multi-modal inputs to deep learning algorithms. This helps detect finer defects and achieve more reliable performance. Fusing sensor data with techniques like 3D reconstruction also allows the generation of detailed point clouds of infrastructure assets. Comparing regular scans of the same site over time enables tracking wear and tear prognostically long before catastrophic failures.
The explainability of ML predictions is also crucial for engineering trust in autonomous systems. Using activation maps and gradient techniques, drone platforms can provide intuitive visual evidence on why particular anomalies got flagged in the inspection footage. This transparency helps technicians verify the detections more quickly to prioritize maintenance efforts. As platforms ingest more images of post-repair assets, the models further improve in accuracy and robustness.
Choosing Components
Flight Controller
The flight controller board is essentially the “brain” of the drone. Using sensor inputs like gyroscopes and accelerometers, it controls and stabilizes the aircraft during flight. When selecting a flight controller, make sure it can support the types of sensors, motors, ESCs and other payload hardware you plan to use. Open-source controllers like Pixhawk offer great flexibility at lower costs. They run ArduPilot firmware which incorporates advanced features like waypoint navigation and auto takeoffs/landing.
Motors and Speed Controllers
Brushless DC motors are the most popular choice for DIY drones today. They have high power to weight ratios making them ideal for multirotors. When picking motors, factors like thrust capabilities, power efficiency, weight and form factor need consideration based on your custom airframe and payload. Electronic Speed Controllers (ESCs) function as interfaces between the motors and flight controller to regulate speeds and deliver the necessary PWM signals. Make sure to get ESCs that can deliver the rated current loads for each motor without overheating or malfunctioning. Higher rated ESCs also allow for growth and adding more payload down the line if needed.
Sensors
Besides gyroscopes and accelerometers embedded in the flight controller, external sensors like GPS modules provide vital functionality for automated flights. GPS improves positional accuracy and enables advanced navigation capabilities like return-to-home failsafe when a drone loses connection with the remote. Other useful sensors include LiDAR, ultrasonic distance sensors, barometers, etc. These give drones situational awareness for stable hovering, altitude hold modes, obstacle avoidance and smooth landing capabilities.
Camera
A key component of any visual inspection system is the imaging equipment. Drones can carry incredibly compact and high-resolution cameras today, even with 4K video capture capabilities. For basic computer vision tasks, a 1080P camera with onboard image processing is sufficient. Wide-angle lenses allow capturing more scene context which is handy for panoramic inspections. Gimbals provide automatic stabilization to counter vibrations and rotations during flight. This keeps the video feed clearer and analysis more reliable.
Field Testing
With the build complete, drones must undergo substantial testing before full deployment. Flight tests help validate flight stability, maneuverability and general airworthiness for safe operations. Ensure all sensor inputs like GPS, gyroscopes produce consistent feeds required for precise navigation over inspection sites. Verify video feeds remain distortion-free across intended operating conditions and camera tilt/angles.
Use sample infrastructure props with simulated damages, leaks, wear, and tear…to gauge model inspection performance. Confidence scores from reported anomalies indicate if further training data is needed. Based on specific environments drones get deployed in, factors like weather, light conditions, and background complexity all impact reliability. Continuously enhance models till the system achieves or exceeds baseline human inspector capability.
Regulatory Considerations
Government aviation agencies have specific operational rules for commercial drone usage. Things like maximum altitude, distance limits, pilot certifications, and platform registrations need compliance depending on countries/jurisdictions. Public liability insurance is mandatory to cover risks associated with aerial inspection drones. Strict protocols must govern data gathering, storage, and analytics – especially when dealing with public infrastructure or private properties. Getting these policy factors right early on ensures the smooth adoption of the technology by industry.
Conclusion
Drones with computer vision capacities will disrupt inspection processes across sectors relying on manual evaluations today. This post provided a blueprint for getting started with building custom drone solutions tailored to unique infrastructure monitoring needs. While DIY builds offer greater flexibility, and there are high-performance commercial drones with inbuilt automation capabilities too. Leveraging robust machine learning toolkits even without extensive programming expertise has been a game changer. With solutions maturing rapidly, drones are set to take over dirty, dull, and dangerous inspection tasks – delivering huge efficiency gains alongside.
Visit our page and contact us to know more.